

Im going to skip the details of the next few steps since they have been covered in earlier post, so if you need info on differential hardening or on the tempering cycles look back a page or 3 and it should fill in the gaps.
I choose to continue with the differential hardening for the larger knives and went with a more tradtional hardening for the smaller knives. These came out great. Had some minor warp in the prototype fish fillet, and some warp in the traditional straight Chefs knife (my fault for laying it uneven on the firebrick)
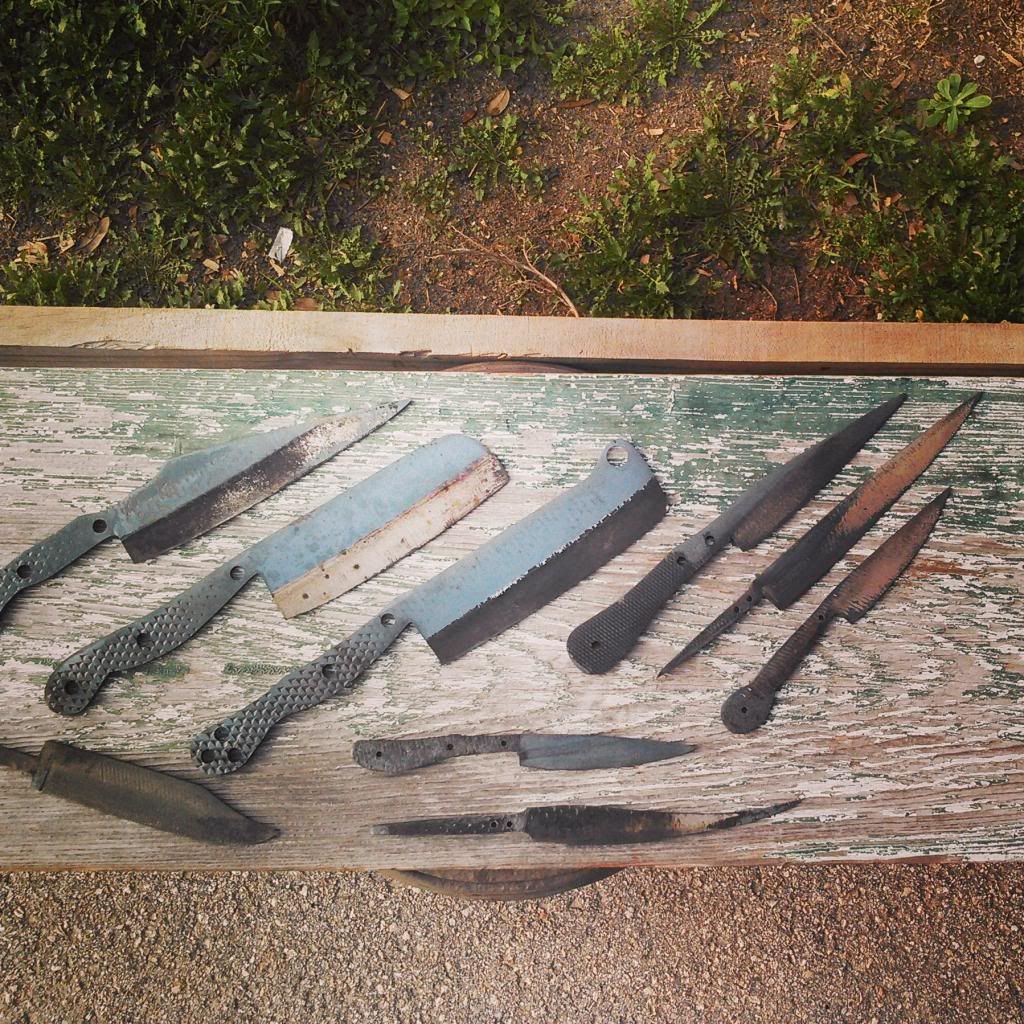
Home they came for the double temper cycle...i was hungry after all the tiring grinding I did while working the horseshow...:LOL:
Theres always room for totts, and hell yes Im going to eat mine naploeon!
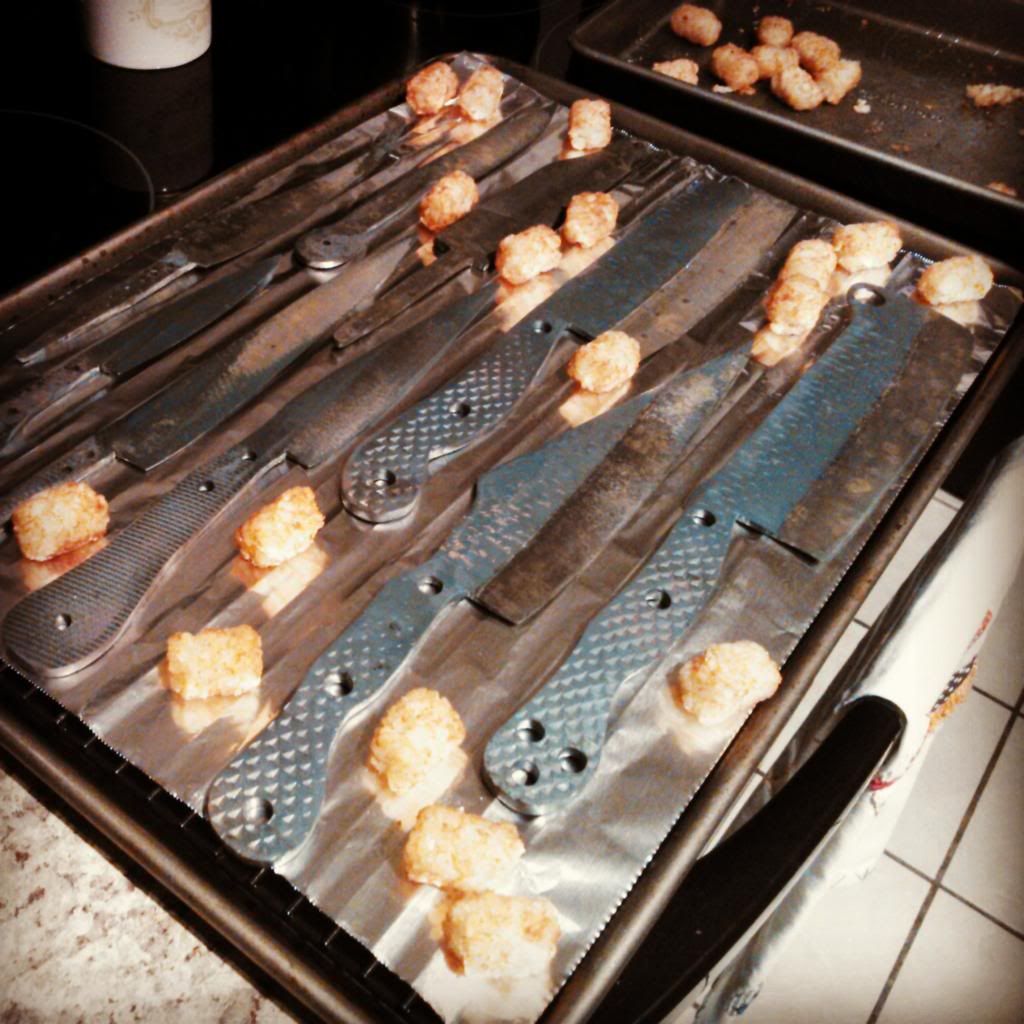
Tempered and back for the finish grinding
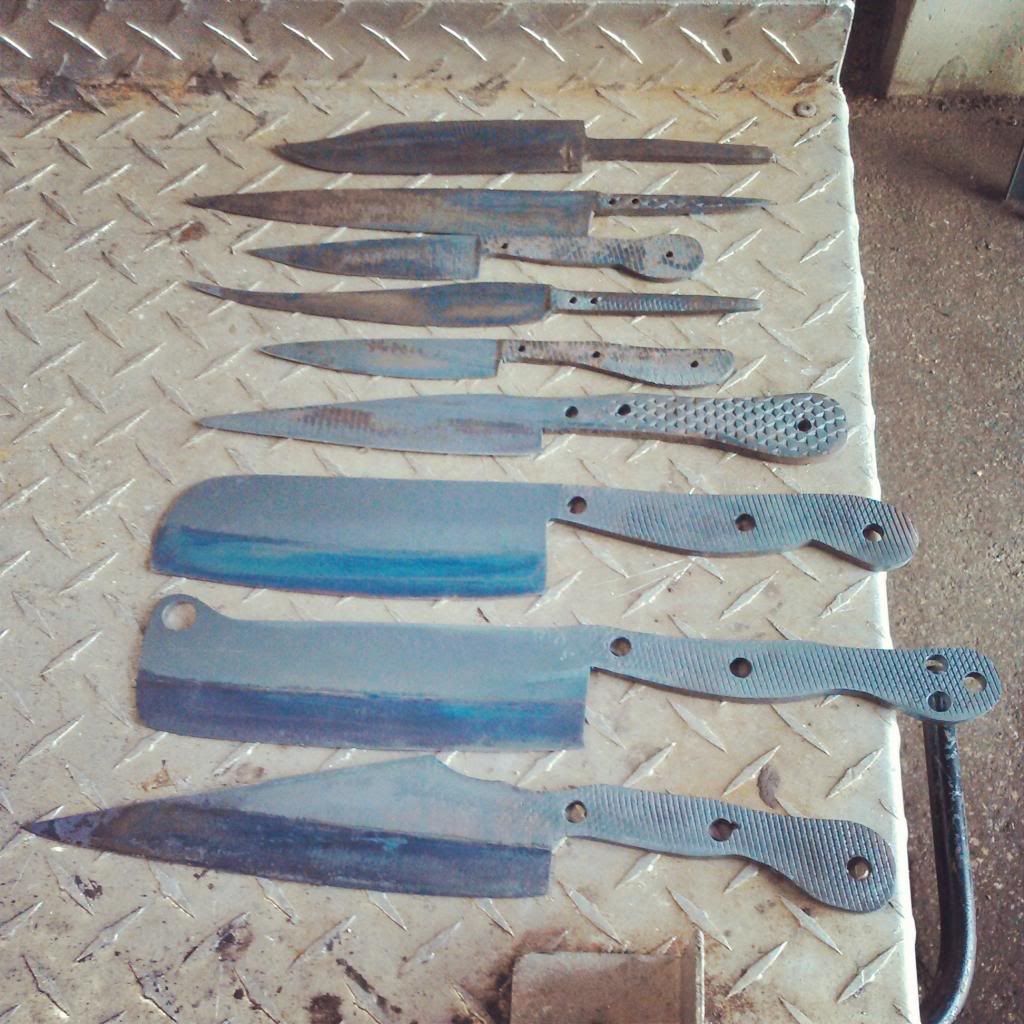
Before I could get started on the final edges and finishes I needed to address the warp in the chef and fillet knife.
The chef knife is extremely thin ground at the tip and even though is was heated slowly enough not to crack the thinner tip was heated first and was able to droop when I lifted the blade out of the forge...I tried to straighten it but I have found that once the metal changes the molecular spacing enough to stretch or bend; it goes right back to the shape you started with as soon as you harden it.
heres an example:
notice the even bow to the blade in the left hand photo and the right hand is after I did some tuning on it. not 100% but a third tempering cylcle should give me the last bit i need.
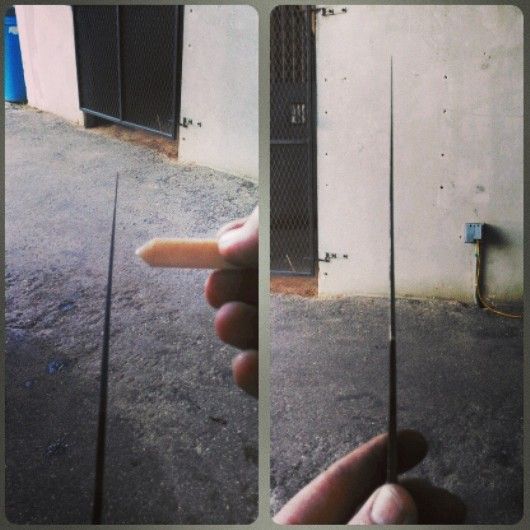
The tuning method is pretty easy but takes alot of patients. NO RUSHING and only try to tweak it after its been tempered.
Use a flat plate (I choose aluminum 1/8" because it transfers heat well)
a handfull of washers and a C-clamp or two.
Just locate the apex of the warp and mark it with a soap stone. Then stack washers evenly spaced off of the apex mark.
Use the c-clamp on the center mark and tighten it enough to hold everything in place.
lastly use the propane torch and heat the apex mark (DO NOT HEAT IT HIGHTER THAN THE 550DEG YOU TEMPERED AT)
once its warmed up compress the c-clamp and overcorrect the bend slightly.
Let it cool and then unclamp, asses the warp and repeat again. each round you will gain a little memory back and eventually it will hold straight.
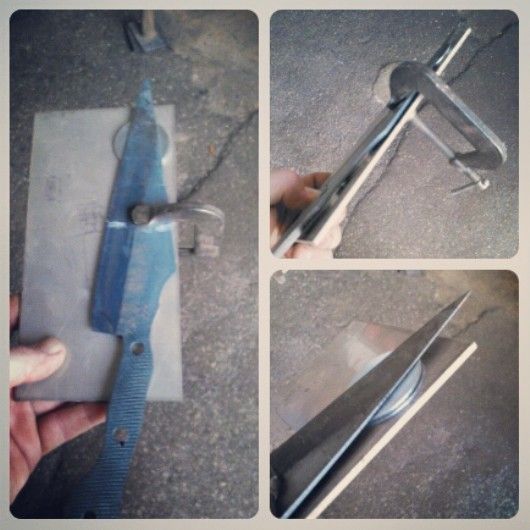
Once I build or buy a heat treating oven I am going to introduce a second normalization to my process. This will occur after the main grinding and before the hardening phase. The general reset that the normalization gives the molecular make up of the steel removes stresses caused buy uneven grinding and forging. These stresses are what cause the warping in the blades. If you harden after the normalization there is no unven pressures to react with and you maintain a straight blade.
So at this point everyone was finish ground and sanded up to 300 grit. I will finish sanding them up to 800 and then various buffer rouges after the handling., but any higher before than handle fitting and glue ups is basicly a waste.
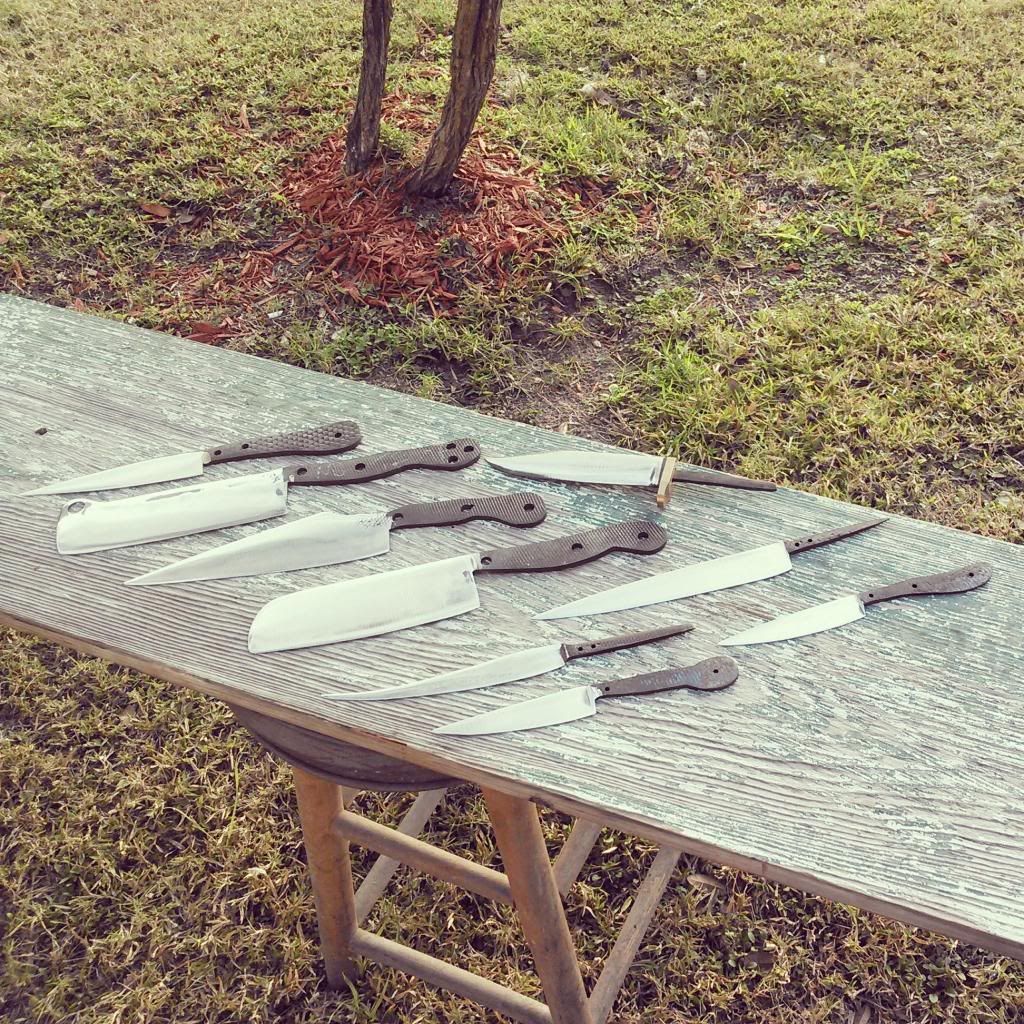
Unfortunalty the handle party will have to wait untill this weekend to start and probably will take me untill next weekend to finish...Im going full out on these with brass bolsters, brass end caps, multi layerd handles, multiwood handles, and three hidden tang handles...one of which is a drop point hunter/skinner with a brass guard, bubinga, walnut, and mule deer antler handle. The hunter blade needs some hand filling work to set the crisp lines at the top of the bevels edge but after thats done and the handle is finished it should be one fancy knife!
Heres the handle mock ups as they were left Sunday night...
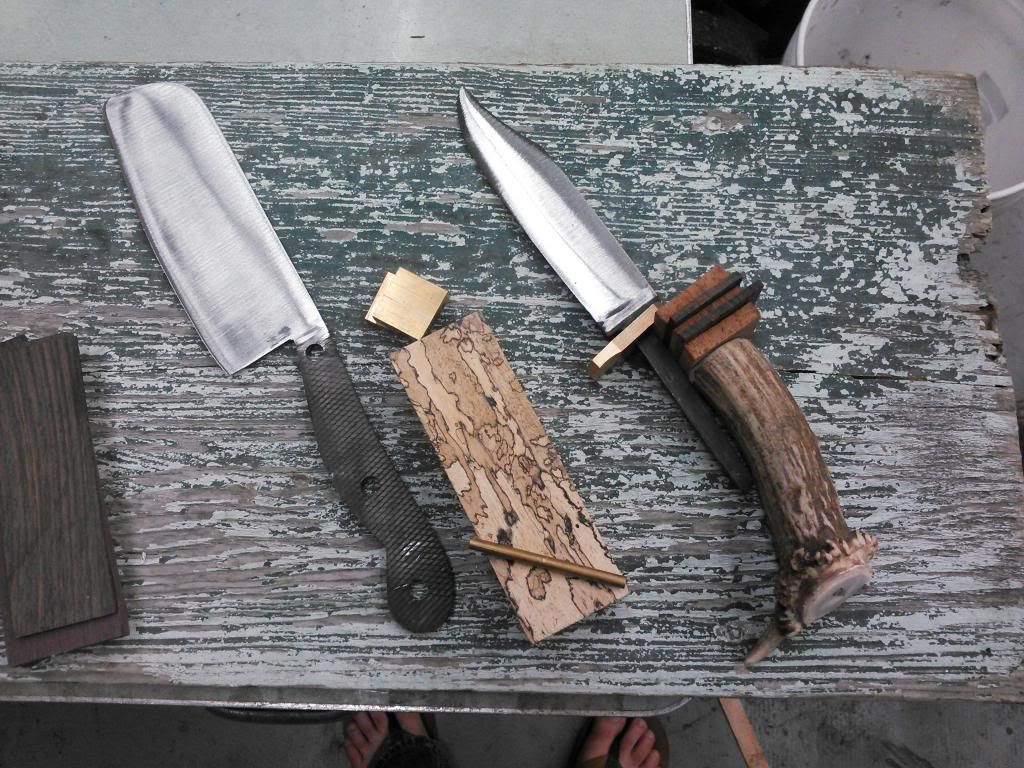
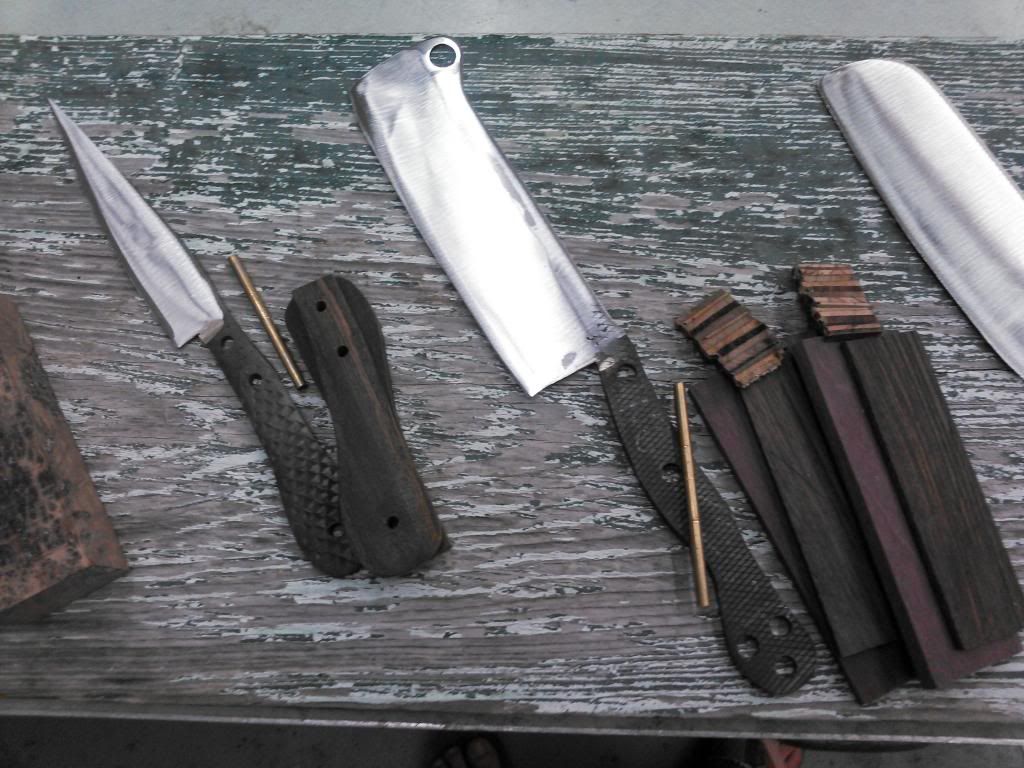
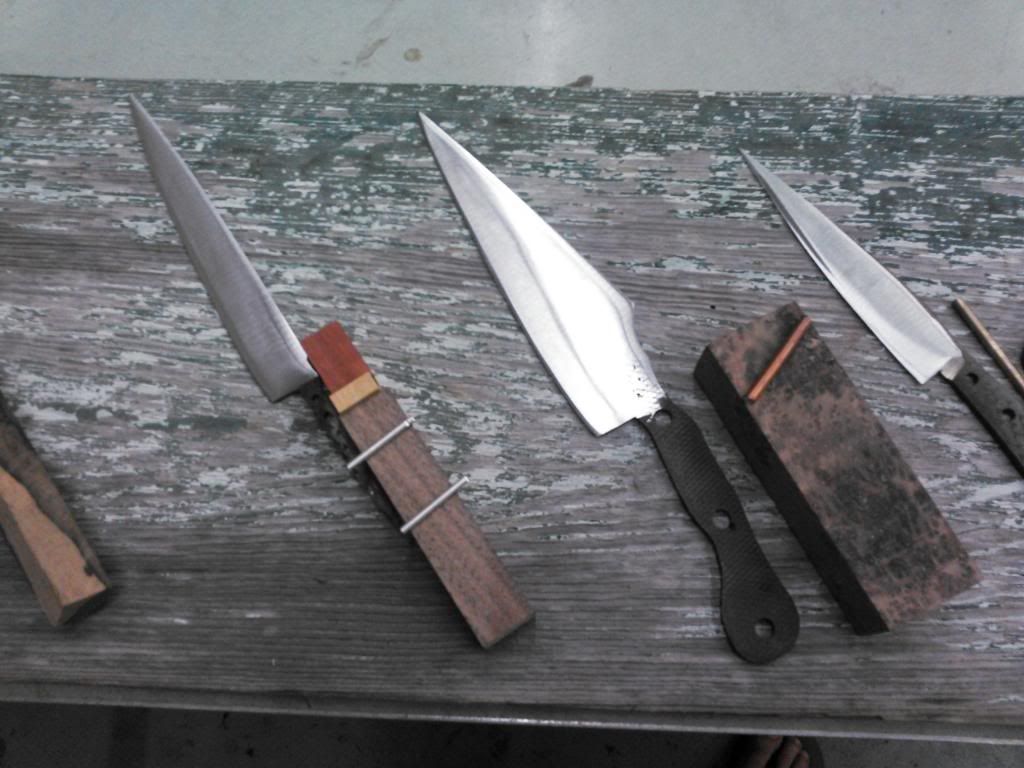
this brass guard will be ground into an oval but i needed the pre-milled slot so this ones getting sacrificed.
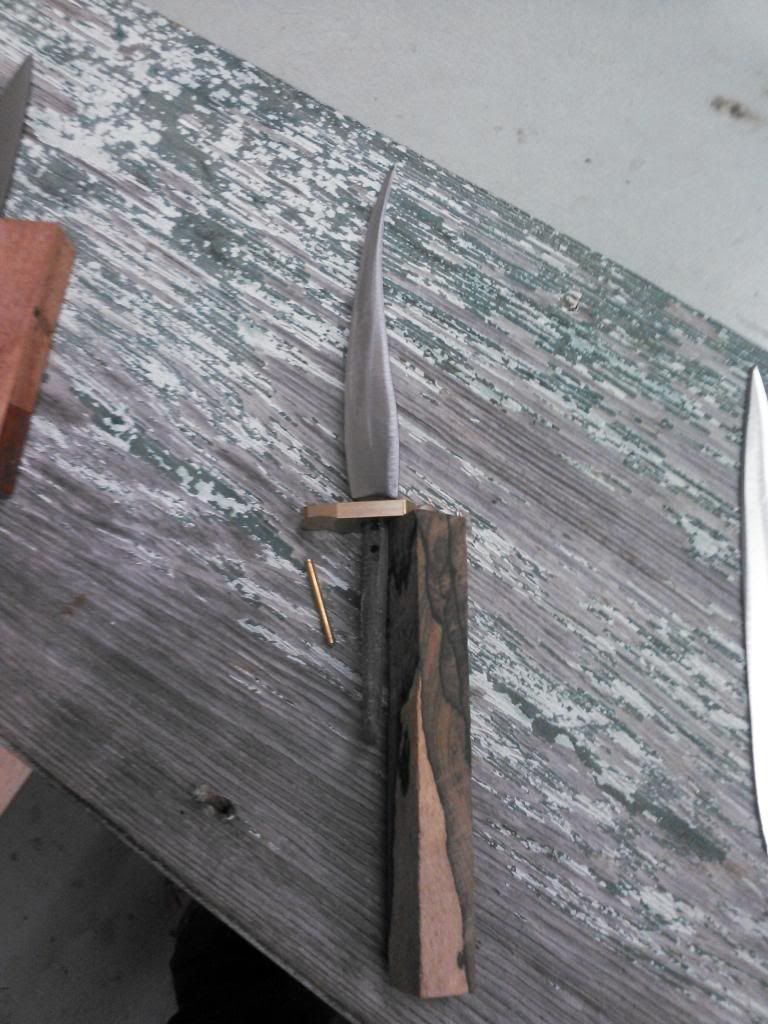
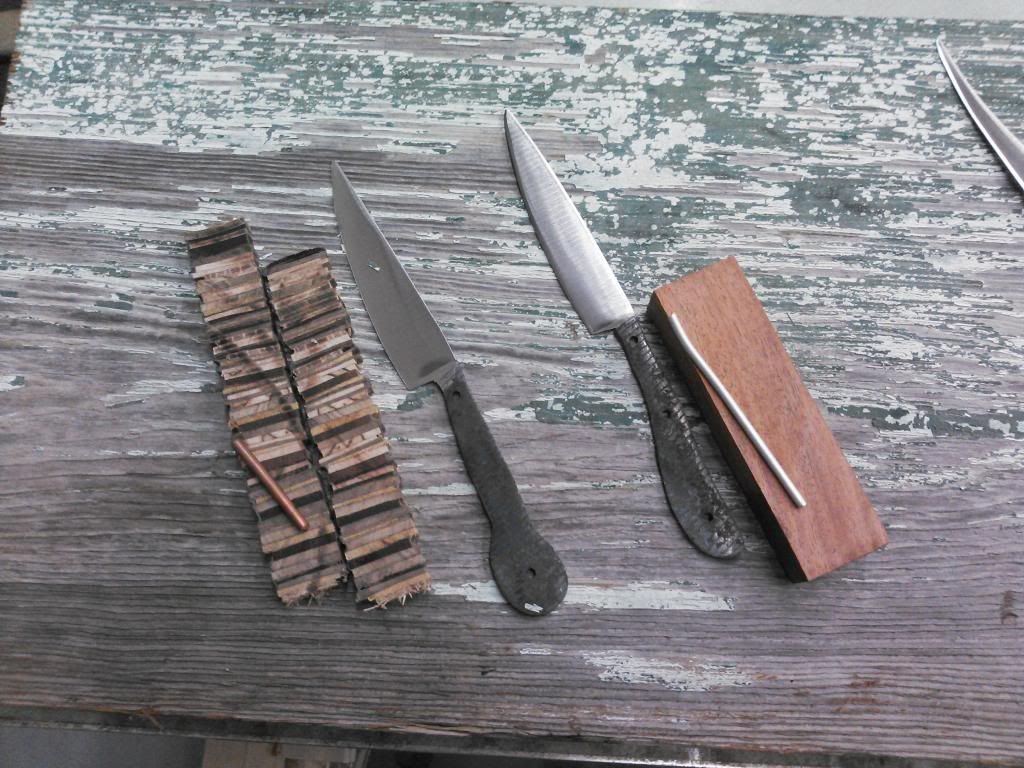
What a journey so far!
Thes first knives I made were - forged, shaped, ground , hardened(ish), tempered(ish), handled, and polished...
These knives are - forged, normalized, cut, shaped, ground, pin holes drilled, preheated, hardened/differentialy hardened, tempered, tempered, uninterupted cooling 3 hours, tweaked, finish ground, handles preped, handles cut and fit, pins cut and fit, assembled, finish shaped, and blade finished....
If you add the second normalization i plan to start doing thats - 20 steps! compared to the 7 steps we started with...
Feels good to be moving forward! :thumbup:
JP
Have a good rest of the week...